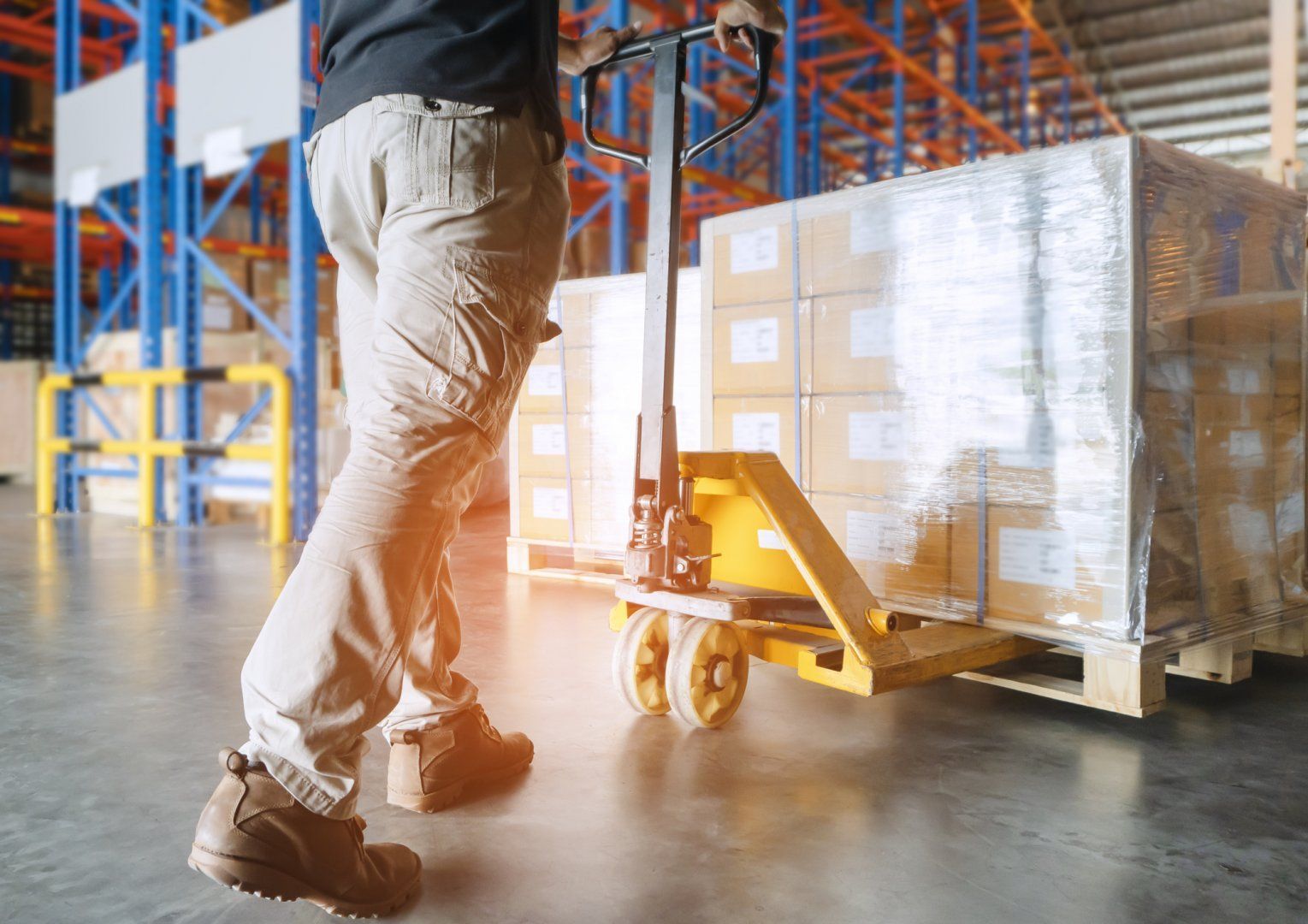
Shipping goods abroad is a complex activity full of challenges, especially when it involves hazardous materials. One of the crucial aspects of this process is the use of certified packaging, but why is this so important?
Imagine this scenario: improperly packaged hazardous cargo could pose risks not only during transport but also to the environment and the people involved.
This is where certified packaging comes into play—a key element to ensure safety and compliance at every stage of transporting hazardous cargo.
What is certified packaging in the context of maritime transport of hazardous cargo?
In maritime transport of hazardous goods, certified packaging plays a fundamental role in ensuring safety and compliance. But what exactly is certified packaging?
Certified packaging meets the requirements established by the IMDG Code (International Maritime Dangerous Goods Code). This code was developed to standardize the international transport of hazardous materials.
Divided into two parts (Volumes 1 and 2), the IMDG Code provides precise instructions for exporters and carriers, ensuring that goods are handled and transported safely and in compliance with international regulations.
For example, if we are exporting paint, the IMDG Code specifies that it must be transported in metal cans, with or without removable lids, depending on the product’s characteristics.
These specifications are detailed in the code, ensuring exporters know exactly how to package and label their goods.
Within the IMDG Code, there is a table for each type of hazardous material, specifying the type of packaging required for each product. Certified packaging is tested and approved by the Brazilian Navy and comes with a certification of approval.
Why should I care?
It’s natural to question the importance of certified packaging in maritime transport of hazardous cargo. Why should it be on your radar? Here’s the critical reason:
Firstly, if the packaging doesn’t comply with IMDG Code requirements, the shipping company will not approve the shipment. This means the cargo cannot be transported, leading to delays and complications in the shipping process.
The responsibility for ensuring goods are properly packaged lies with the exporter. It’s essential that the exporter understands the IMDG Code standards and follows the guidelines for packaging and labeling hazardous cargo.
However, often the exporter’s representative may not have the technical knowledge required to ensure compliance with the IMDG Code. This is where NVOCCs, such as Allink, come in, providing guidance and clear instructions to ensure documentation aligns with regulations.
Allink acts as an intermediary between the shipping company and the exporter in obtaining IMO approval. However, the responsibility for ensuring the packaging is suitable for IMO shipping rests with the exporter, who must be familiar with IMDG Code standards.
Upon receiving the customer’s documentation, Allink’s IMO department conducts a preliminary analysis, checking for any discrepancies or inconsistencies in the declared packaging.
In many cases, the customer’s representative may not be aware of the rules and requirements for hazardous material packaging, which is why we always make ourselves available to assist in interpreting the standards and helping with necessary corrections for approval.
It is important to emphasize that it is the responsibility of the exporter and/or the responsible chemist to have knowledge of the IMDG Code standards for transporting hazardous goods.
The role of the NVOCC is to analyze the documentation and guide the customer on any discrepancies or inadequacies pointed out by the shipping company.
For example, if a customer submits a can of paint stating that the cargo is packaged on a pallet, Allink’s team must inform them that the pallet is not considered suitable packaging for paint, except in specific cases, such as batteries.
Therefore, ensuring the use of the appropriate certified packaging for hazardous goods is critical to guaranteeing safety for those handling the cargo and for the chosen transportation mode, whether road, sea, or air.
Risks of incorrect packaging in IMO transport
The implications of not using certified packaging for hazardous materials can be severe and far-reaching, impacting not only operational safety but also leading to significant legal and financial consequences.
The use of improper packaging increases the risk of leaks, spills, or even explosions during transport, posing a threat not only to workers but also to the marine ecosystem and coastal communities.
It’s important to emphasize that safety is the primary concern when it comes to hazardous cargo packaging. Improper packaging can pose serious risks to the health and safety of workers handling the cargo during transport and at terminals.
Beyond safety concerns, failing to use certified packaging results in the shipping company refusing to load the cargo. Without shipping approval, the entire logistics process is interrupted, leading to delays, additional costs, and potential damage to the exporter’s reputation.
Reusing packaging: Is it allowed?
Reusing packaging for hazardous materials is strictly prohibited due to the significant risks it poses to the safety of workers, the environment, and the cargo itself.
While it might seem convenient, reusing packaging for hazardous products can result in severe and even fatal consequences.
Reusing packaging can lead to cross-contamination of products, causing dangerous chemical reactions or explosions. Even if the packaging appears similar or has been “cleaned,” residual chemicals may remain and interact with new materials, increasing the risk of accidents.
Another critical point is that hazardous material packaging is certified for single use only, and reusing them violates these certifications. Certified packaging undergoes rigorous testing to ensure safety and compliance with regulatory standards.
Reusing packaging compromises this compliance and may result in the shipping company or port authorities rejecting the shipment.
It’s essential to understand that safety is the top priority when transporting hazardous materials. Any attempt to reuse packaging for hazardous products represents an unnecessary risk to all parties involved and must be avoided at all costs.
Re-exporting cases: How to proceed
When dealing with re-exporting cargo, especially hazardous products, it’s essential to follow strict procedures to ensure compliance and safety throughout the process.
At Allink, we handle various re-exportation cases, and it’s crucial to adopt careful measures in collaboration with shipping companies to ensure a successful operation.
When a client requests the re-export of hazardous cargo, our team carefully reviews all necessary documents and certificates to ensure the operation is conducted properly.
Firstly, we request the client’s international certification of the packaging, issued by the competent authorities and certifying the packaging’s compliance with regulatory standards.
We also request detailed photos of the packaging to be re-exported. These photos are crucial for visually verifying that the packaging matches the provided certification.
We compare the codes and characteristics in the certification with those on the packaging in the photos to ensure it’s the same batch and complies with regulations.
By following this procedure, we ensure that re-exportation is conducted safely and in compliance with legal and regulatory requirements. This provides peace of mind for both the client and those involved in the operation, reducing the risks of shipment refusal or issues during transport.
Thus, when handling re-exportation of hazardous goods, it’s essential to follow a careful process of verification and validation of documents and packaging, ensuring safety and compliance at every stage of the operation.
Want to dive deeper into the subject? Check out how to handle international transport of hazardous materials by sea.
Continue a navegar no blog da Allink
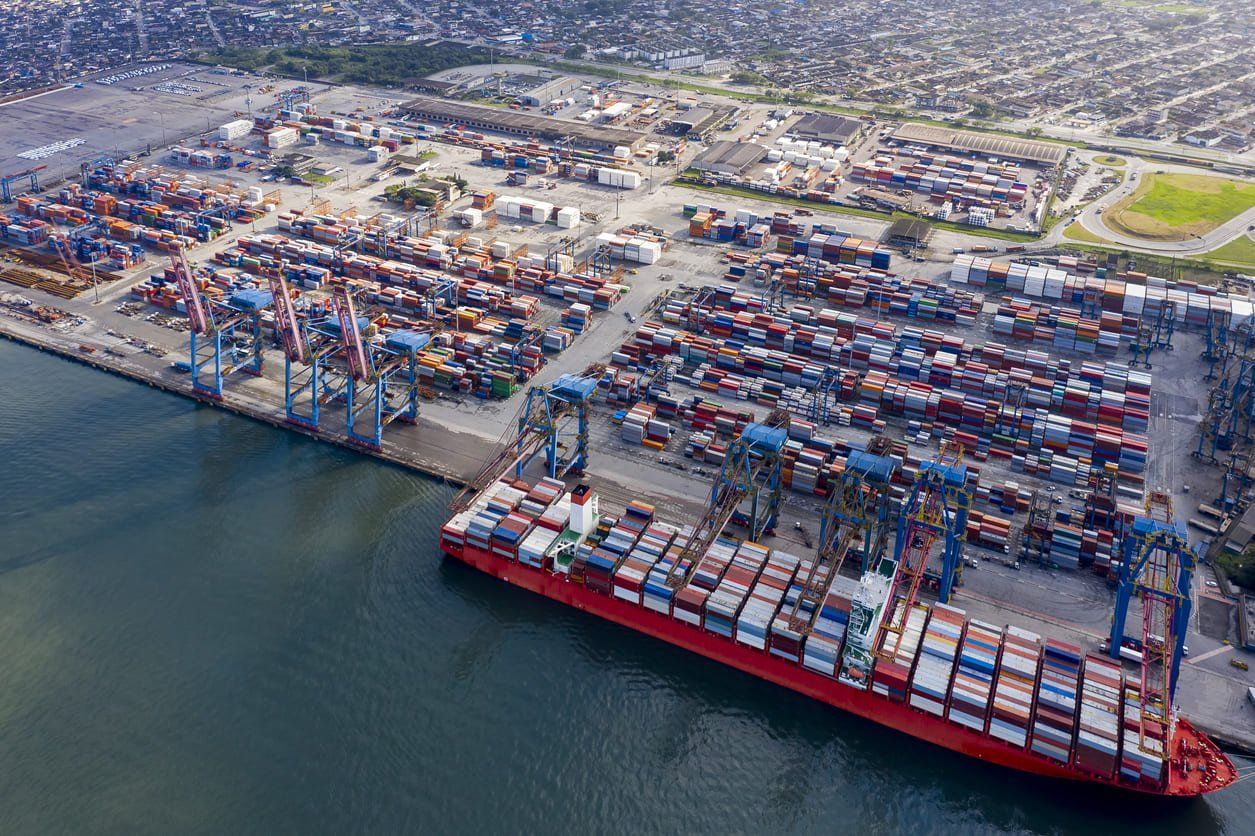
Mantenha-se informado sobre o comércio exterior
Assine nossa newsletter e receba atualizações semanais de forma gratuita sobre o mundo da logística.